Kanban in the Kitchen: a Recipe for Supply Chain Education
The supply chain is for smart people. Not too many people understand the basic concepts, let alone the more sophisticated approaches and ideas. Supply chain professionals always try to promote and share what they are doing, but their presentations are usually met with glossy-eyed stares. What we are trying to do is extremely complicated, so unfortunately people just don’t get it. HOGWASH!
The supply chain is one of the most simple, easy-to-explain functions around. The supply chain has one simple goal—to fulfill product and service demand effectively and efficiently. And the activities are not some theoretical construct; the supply chain always ends up with physical products that are bought, made, moved, and stored. Yes, some of the strategies and processes become complicated. Still, they can always be tied back to the real world. For a broad audience to understand (and support) supply chain management, they need a very practical education with tangible example. For that, all you have to do is go to the kitchen.
I tried this education with someone who is probably the furthest away from supply chain management—my mother. My mother has been a homemaker for over 30 years; she is a smart woman who runs the household (and my father) like a business. Would she understand supply chain concepts?
I started with her shopping list. What was she planning on getting from the supermarket? Bread, turkey, cheese, potatoes, chicken breast, one quart milk, Cheerios, asparagus, tomato soup. How did she decide what to get? Well, she was planning on serving leftovers tonight because they would be out all afternoon. Dinner the following evening would be chicken with asparagus and mashed potatoes. Lunch tomorrow would be sandwiches and soup. And of course, father has cereal for breakfast each morning. And why go today? Well, it was going to rain tomorrow, so she didn’t want to drive in wet weather.
“Mom,” I said, “You are a supply chain expert.” She looked at me as if I was ten years old. “Seriously, you are. Let’s look at all of the things that you did. First, you figured what the demand for food would be—that’s forecasting. Fortunately, your customer, Dad and yourself, will consume whatever you make. Then you decided how and when you were going to your meal—that’s production scheduling. You knew that today wouldn’t be a day to cook, but you already planned out tomorrow’s menu.”
“Then, you figured out the ingredients that you needed—that’s material requirements planning. You mentally went through your meal plan and figured out what ingredients went into each. We call that a Bill of Materials explosion. I noticed that you didn’t put mustard or mayonnaise on your list. I am guessing that you already have enough in the refrigerator to last you a while, so no need to buy more. And you are buying tomato soup, although I see that you already have one in the cupboard. I know what you always say; it’s always good to have an extra can for a rainy day. In my world, that’s inventory management with safety stock rules built in.”
My mother thought for a moment, then laughed and messed my hair. “I’m glad that we are both supply chain experts, even if you do need a lot of fancy names for all of the things that I do normally. Will any of these fancy ideas actually help me to do anything better?”
We talked for a few more minutes about where she could improve. I looked through the cupboards and found a lot of extra cans of soup and other goods. I rearranged the cabinets to have a spot for each item and threw out some of the old (obsolete) products. Then we talked about how many cans of tomato soup she needed at any one time. We wrote a card under each can that said “Buy 1 can of tomato soup”. As she used that can, she would pull the card as use it as part of her shopping list.“
I like this little setup, son,” my mother said as she smiled. “What do you call this?”
“It’s called Kanban, Mom. It a Japanese inventory and replenishment technique.”
“Can-Ban: got it, works great for cans. I can’t wait to tell my friends down at the gym about how my son is so smart.” She gave me a big hug.
“I’m sure they will appreciate it,” I replied. “Oh, and Mom, about Sunday dinner this week. You know that I love meatloaf, but maybe Dad would appreciate something different. Maybe we should talk about managing New Product Introductions.”
My mother smiled and shook her head. “That time you almost got me. Your father wants something different than meatloaf? Now you’re dreaming.”
Oh well, I guess that some things don’t change.
Copyright © 2006-2007 Hawkeye Planner LLC. All rights reserved.
Monday, November 26, 2007
Kanban in the Kitchen: a Recipe for Supply Chain Education
Saturday, November 17, 2007
Foreign Flashback:Nissan 180SX Manufacturing in Japan
This video is completely in Japanese and is well over 10 years old, but it is still interesting to see how the Nissan 180SX (S13 chassis) was manufactured. Production for the car began in 1989 and ended in 1998. If I had to guess, this video is probably from the early 90's. As you watch the video note that virtually everything is performed manually by the production workers including welding and glue application/window placement.
Cutting Edge: Intel's Fab 32 (Arizona)
"When completed, Fab 32 will become Intel's sixth 300-mm wafer facility. The structure will be about 1 million square feet with 184,000 square feet of clean room space. The project will create up to 1000 new Intel jobs at the Arizona site over the next several years. During the construction phase, more than 3,000 skilled trades people will be hired to work on the project.
Intel currently operates four 300-mm fabs that provide the equivalent manufacturing capacity of about eight 200-mm factories. Those factories are located in Oregon, Ireland and New Mexico. The company also has an additional 300 mm fab currently under construction in Arizona (Fab 12) scheduled to begin operations later this year, and one expansion in Ireland (Fab 24-2) scheduled to begin operations in the first quarter of next year.Manufacturing with 300-mm wafers (about 12 inches in diameter) dramatically increases the ability to produce semiconductors at a lower cost compared with more widely used 200-mm (eight-inch) wafers. The total silicon surface area of a 300-mm wafer is 225 percent, or more than twice that of a 200-mm wafer, and the number of printed die (individual computer chips) is increased to 240 percent. The bigger wafers lower the production cost per chip while diminishing overall use of resources. Three-hundred-mm wafer manufacturing will use 40 percent less energy and water per chip than a 200-mm wafer factory."
Thursday, November 15, 2007
Car & Driver: VW's Transparent Factory Tour
Sunday, November 11, 2007
Semiconductor Manufacturing Revisited

I have spent some time inside cleanroom environments, and they are quite an interesting place to be. The machinery is very expensive costing in the millions of dollars for many tools, and the air generally contains less than 10 particles ≥0.5 µm (microns) in diameter (200 times smaller than the size of a human hair). In layman's terms: If you have a job in which you work inside a cleanroom and you go to work and have allergies that morning, you will feel great inside the cleanroom because there are no particles

The last bit of information worth adding about semiconductor manufacturing is that it is a very complex environment from a production control perspective. Many products in the world are made by batch processes such as paper, chemicals, Coca-Cola, etc. On the other hand many products are made in discrete units with a lot of 1 (Cars are a good example). Semiconductors wafers are generally run together as a lot, but you sometimes split or merge wafers from that original lot and to a secondary lot. Additionally, in

So on to the articles:
How Chips are Manufactured brought to you by Hardware Secrets
Semiconductor Production 101brought to you by Tom's Hardware
Friday, November 9, 2007
Direct from Dell.... (Austin, TX)
I happen to have studied Dell very closely since about 2001, and I was lucky enough to attend many presentations by Dell employees (and even know several). A few things to note are that as of 2004-2006 Dell operated under the following structure:
- Laptops are made overseas (generally in Taiwain) by ODMs and air freighted to the US. This likely is due to labor savings and the density to price ratio.
- Dell's Topfer Manufacturing Center in Austin, TX (TMC is building PN2) assembles Desktop PCs while the building next door (PN1) builds servers.
Additionally, since this video was made many changes have been implemented at TMC:
- Barcode scanning has been changed to RFID on the totes that move around the factory.
- Inventory is kept low because Dell does not keep a component inventory warehouse themselves. Their components are kept at consignment warehouses next door where the suppliers own the inventory until it is pulled for a customer order.
- The Boxing line is still performed manually in some instances, but for certain platforms the High Velocity Kitting line completes the process via automation.
Thursday, November 8, 2007
Facility Showcase: BMW Leipzig
Wednesday, November 7, 2007
Maserati: Italian Luxury
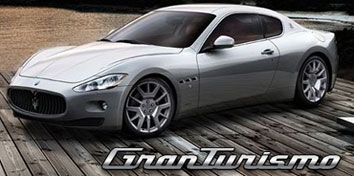
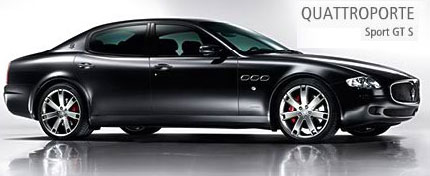
- Quattroporte - Four Door sedan (Quattroporte means four doors in Italian)
- GranTurismo - Hard Top Coupe (2+2)
- GranSport - Hard Top Coupe (2+2)
- Gransport Spyder - Two Seat Convertible; No back seat
- Coupe - Hardtop Coupe (2+2)
In fact, per the video the only difference between the the Quattroporte and Granturismo is that the Quattroporte has a larger grille. Maserati only manufactures ~7,000-10,000 vehicles per year, but would like to increase that number as sales in North America increase.
Some interesting points from the Maserati Plant Tour video that I noted as I watched it were that:
- Maserati has implemented a JIT methodology, and looked to have much of their information on the Paper travelers that move with each car.
- Around the 3 minute mark the spokeswoman notes that the vehicle being shown is definitively an american car because of the cup holders!
- Engines are tested as modules by Ferrari and also Final Tested in a finished car up to 250 kpm. Each car is then driven 80km over city streets, mountain roads, and highways.
- If you pick up your car at the Maserati showroom you will find your car covered with a blue cover so you can unveil your car, open your champagne, and party with Maserati! You also get your own photographer so you can be assurred the event is documented. Note: Sounds very similiar to Ferrari to me!